Peavey Chapter Five
Peavey: Reinforcing the Weak Links
Chapter 5
“If we do the same things tomorrow that we did today, we will know what to expect in the future — status quo or worse.”
Hartley Peavey was on the road one weekend in the early 1970s when he stopped by a bar in Gulf Shores, Alabama. A solo act was performing, and while the artist was a talented singer, his PA system sounded awful. Hartley asked to see the performer’s gear and was shocked to see that the mixer was a Peavey product. He helped the performer make adjustments to the mixer, which made him sound much better.
Problem solved, but the experience made a lasting impression on Hartley.
At first, Hartley was annoyed that the dealer hadn’t explained to the performer how the equipment worked. However, he soon realized that it was his own fault. The real problem was that Peavey was not doing enough to educate dealers, and the solution was to develop a training program.
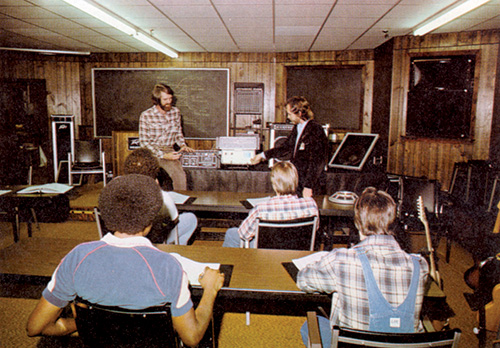
The first Peavey Factory Seminar program commenced in early 1975. Peavey began bringing in retail dealers, educating salespeople on the physics of sound, and showing them, in side-by-side comparisons with competitors’ products, how these concepts translated into the performance of Peavey products. The classes were led by Peavey employees Hollis Calvert, who covered musical instrument products, and Marty McCann, who assisted with sound reinforcement training.
The seminars, which continue today, set the foundation of a loyal, trusting relationship between the manufacturer and dealer. Hartley reinforced his policy of “one fair price for everyone,” which allowed small dealers to compete against retail giants on a more equal playing field.
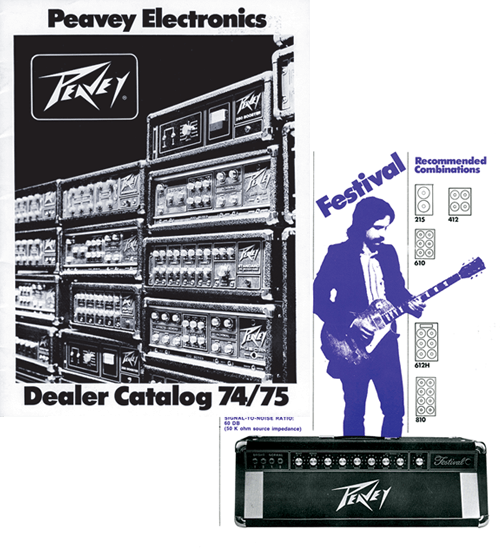

Speaker Innovation Accelerates
By 1975, the first phase of Peavey’s Plant 3 project was operating, and most of the cabinetry and metalworking production had been transferred from Plant 1. Amplifier innovations at this time included a new Festival twin-channel head, with aluminum trim strips that matched the cosmetics of the speaker enclosures; the 160W Mace combo (212 or 412); and the 120W 112 Artist model.
These units were hybrids, with solid-state front ends and 6L6 tube power amps with excellent tonal range. Sales of these units soared, as the models offered the flexibility of Automix, which was revolutionary for twin-channel amps at the time.
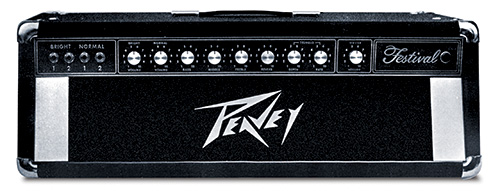
Meanwhile, Peavey’s PA line continued to evolve with HF tweeters replacing horns in the column speakers. The tweeters were offered as high-frequency components in T-300 (three-tweeter) and T-12 (12-tweeter) configurations.
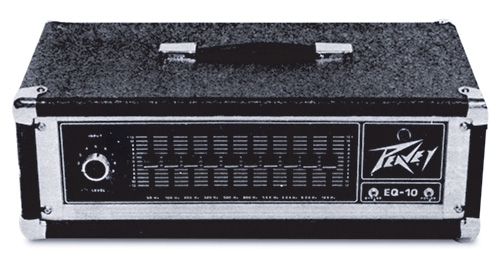
Product innovations included:
- 1210-TS and 1210-T column speakers
- 112-TS enclosure, a slant wedge design representing an upgraded Monitor enclosure
- 1200 mixer along with Peavey’s first signal processor, the EQ-10
- 115HT and 215HT Vocal Projector sound-reinforcement speakers
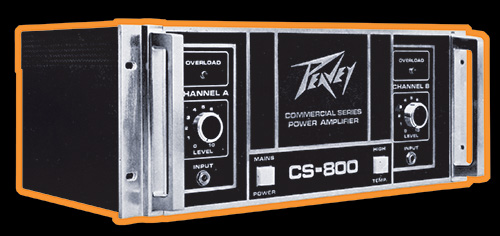
Additionally, in 1976, the CS 800 power amplifier was introduced, offering 400W per channel and electronic-crossover modules that allowed for easy bi-amping. The CS 800 became an industry standard thanks to its innovative design, high power, and relentless reliability.
At this point, there were so many new products rolling off Peavey’s line that Hartley resorted to buying a printing press so the company could save money on its own product literature.
Necessity: The Mother of Invention
Back in 1974, Peavey had achieved an industry first when it introduced the MF-IX horn. It was designed by engineer John Gilliom, formerly of Electro-Voice, at a time when EV’s owners, Gulton Industries, didn’t want to invest in the tooling to make the unit. Gilliom approached Peavey, explaining how to design a superior horn without infringing on his own patent. Hartley realized the potential and hired Gilliom, who stayed in Meridian for several years and helped build Peavey’s transducer business.

By this time, Peavey’s new power amps, CSP speaker system, and increased power ratings of guitar and bass amps were pushing speakers and drivers to their limits. Competitors offered premium speaker options to address this problem, but they had reliability issues and a high cost of re-coning. When suppliers were unwilling to respond to demands for improvements, Peavey began an in-house transducer research program. At Hartley’s insistence, the R&D team’s mission was to create a premium horn driver and die-cast chassis speaker with field-replaceable cone/voice-coil assemblies, allowing for field replacement of the blown voice coils.
Historically, the loudspeaker is the weakest link in the audio system, which is why Peavey and competitors were spending huge amounts of money to improve loudspeakers. In Hartley’s view, it seemed reasonable to design premium transducers utilizing “field replaceable” diaphragm assemblies. This has been common practice with high-frequency drivers for decades, but the concept had not yet been applied to cone-type loudspeakers. Although it cost Peavey $5 more per unit to make the speakers this way, Hartley wanted Peavey products to be as customer-friendly as possible.
“As I often remind people, from a car radio to the largest concert sound system, the loudspeaker is the first thing to go should the volume be cranked up all the way,” Hartley explained. “Having the ability of repairability instead of being tediously ‘reconed’ is a huge advantage offered by Peavey.”

As fortune would have it, two ex-EV employees arrived saying they wanted to start a speaker factory. They called their partnership “The Spider Works,” and they completed the team for Peavey’s next big innovations.
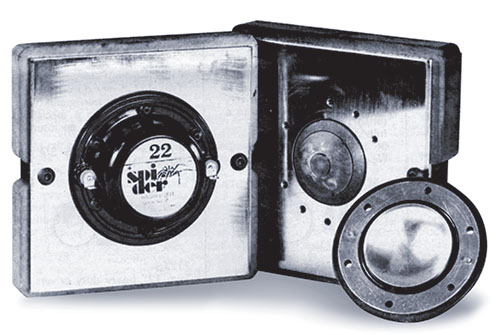
Black Widow Brings ‘Field-Replaceable’ to Life
Peavey R&D worked with John Gilliom to create the Model 22 Driver in 1976, which first appeared in the Spider System (SP-1) to complement Gilliom’s horn. The high frequency driver was called the “22” because it had a 2-inch dome and a 2-inch voice coil. Master machinist Sam Moore formed a one-piece aluminum-dome diaphragm for the 22 at field-replaceable tolerances.
Soon after, the Model 22 Driver was spun off on a new chassis speaker, and the Spider series Black Widow speakers were spawned. The Black Widow featured a number of revolutionary design concepts, including Hartley’s concept of a detachable magnet-and-cone assembly, which allowed for replacement of a blown speaker cone in minutes.
The Black Widow also introduced the concept of a 4-inch voice coil of edge-wound aluminum ribbon wire, which allows for 24 percent more wire to be wound on the voice coil, in effect concentrating more energy for greater power handling. The design represented a monumental advance in transducer technology. As a result, a large portion of Peavey’s Plant 1 converted to Black Widow speaker fabrication.
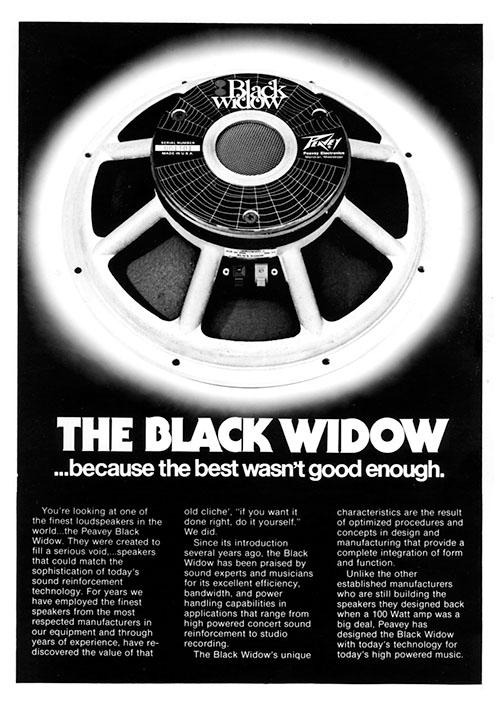
By the mid-1970s Peavey was setting itself apart from competitors with drastically enhanced performance from both amps and speakers. Now that consumers had a variety of reasonably priced solutions, market demand was leading to affordable, better-sounding instruments — and a new opportunity for category expansion at Peavey.
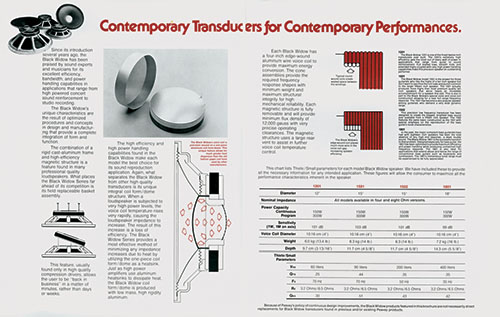